By Tyrone Burke
Students on Carleton’s CU InSpace team are reaching for the stars – or at least taking a solid first step. This team of undergraduate students designs, engineers and builds high-powered rockets for intercollegiate rocket engineering competitions like Launch Canada and the Spaceport America Cup in New Mexico. It consists of approximately 100 students, and is currently working on a rocket for the 2023 competition season.
Its members have devised a way to supercharge a rocket with an innovative design for a hybrid rocket engine test stand that lowers the system’s weight and increases a rocket’s thrust. They presented their findings at the Space Propulsion Symposium of the 73rd International Astronautical Congress in Paris in September 2022.
A hybrid rocket uses propellants that are in two different physical states – one as one liquid or vapour and one as a solid. This type of rocket is often used by student groups because the design helps prevent the mixing of volatile liquids, and the explosions that can potentially occur when this happens.
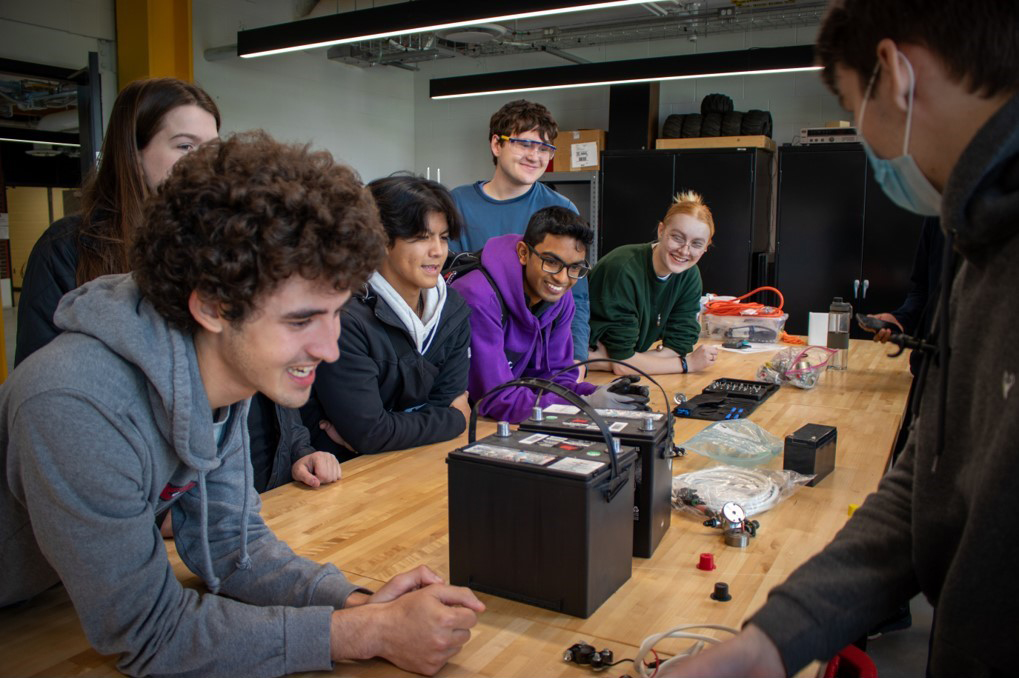
CU InSpace’s propulsion team working on their rocket’s propulsion system.
The paper that the team presented in Paris was authored by Brendan Griffin, August Lear, Simon Golla, Nykoda Cooper and Philip Hagerman, and it use computer modelling to show the propulsion that can be achieved by injecting gas to their system to maintain its pressure, and sub-cooling one of their propellants.
“The CU InSpace rocket uses a solid fuel and a liquid oxidizer,” says Brendan Griffin, a student in Carleton’s Aerospace Engineering program, and the co-president of CU InSpace. “That is slightly different from rockets launched by space agencies, which typically use two liquids. We use paraffin wax as a solid fuel, and nitrous oxide as an oxidizer.”
“These materials can be easily stored, and nitrous oxide will vaporize until it reaches its vapour pressure, which is pretty high. It basically self-pressurizes, so we do not need a pump to move the propellant from the tank into the rocket. That reduces the system’s complexity.”
But the CU InSpace team saw an opportunity to improve performance by injecting gas into the oxidizer. They conceived of a design, and obtained feedback from faculty at Carleton, and Adam Trumpour, an engineer and the President of Launch Canada.
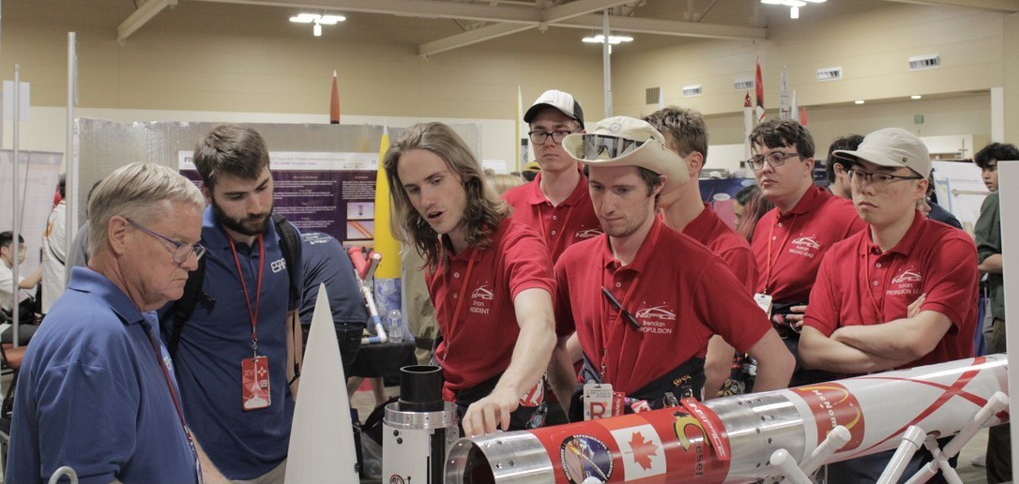
CU InSpace at the 2022 Spaceport America Cup in New Mexico.
In the CU InSpace hybrid rocket engine test stand, nitrous oxide is stored in a metal cylinder – similar to what you might find at a dentist’s office. And as nitrous oxide propellant decreases, the pressure in the tank does too. But by injecting it with gas from an external source, the pressure can be maintained for longer, and a rocket can generate more thrust.
But the students went further than that. They propose injecting gaseous nitrogen into the top of the propellant tank to achieve higher pressures in the tank, and keep the system stable throughout a launch.
“Instead of allowing the nitrous oxide to vaporize and fill the tank, we have proposed to do it with another gas like nitrogen instead, which opens possibilities for increasing efficiency,” says Griffin.
“You can achieve even higher performance using a technique called sub-cooling. To do this, the tank is chilled externally with a substance like dry ice. This can cool the nitrous oxide as low as -40°C — well below its boiling point.”
“This increases its density as a liquid, and would allow you to use a smaller tank to get the same results. We determined that if we can successfully pressurize that way, we can get a mass reduction of between five and fifteen per cent. It could also extend the burn time of the engine, which could generate more thrust.”
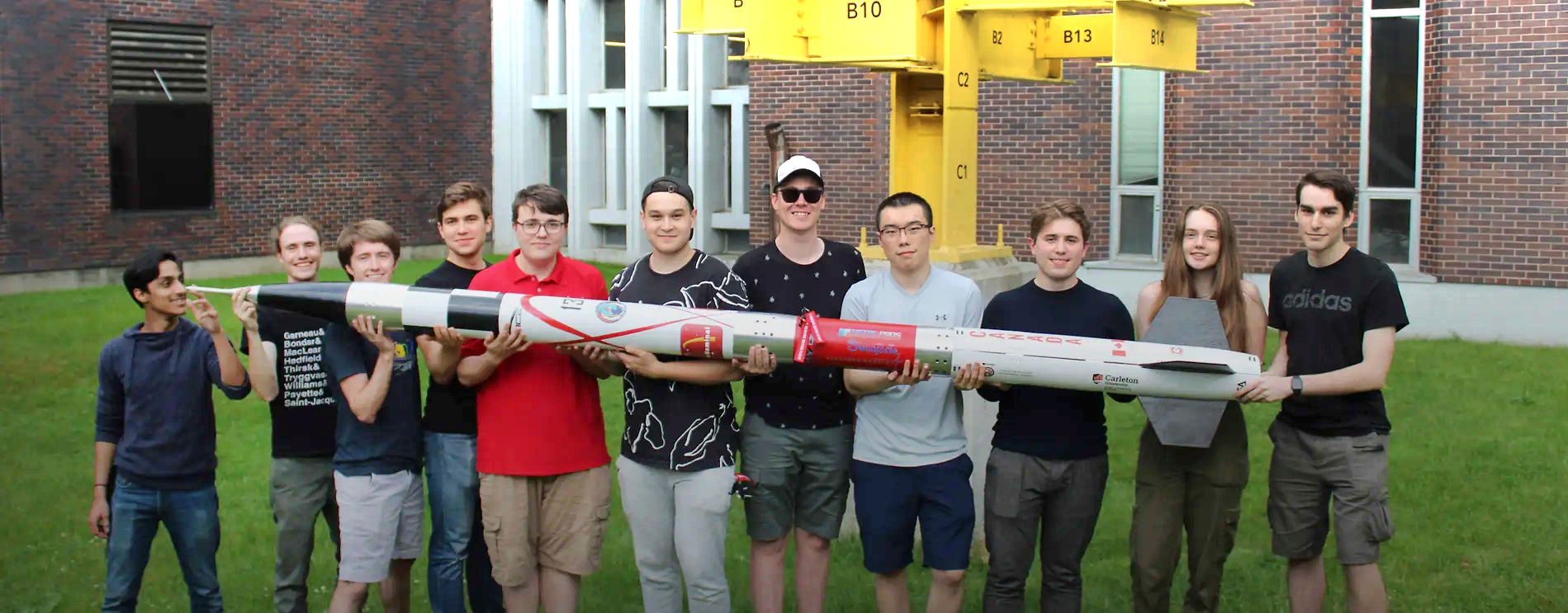
The CU InSpace team used computer modelling to show that these techniques could increase the system’s thrust considerably. When the nitrous oxide self-pressurizes, the system’s thrust is 4.2 kilonewtons (kn), but when it is injected with nitrogen gas, that increases to 6.1 kn, and when the propellant is sub-cooled, it increases again to 6.6 kn.
“We are working toward a test, and beginning to look for suitable sites,” says Griffin.
“There are obviously safety considerations when testing a system like this, and we are looking a site that can provide a 300-metre radius around the launch site. There are safety features built in to the system, but you still can’t do this anywhere near people.”
Monday, October 24, 2022 in Aerospace, Competitions and Awards (External), Experiential Learning, Feature Stories, Undergraduate
Share: Twitter, Facebook